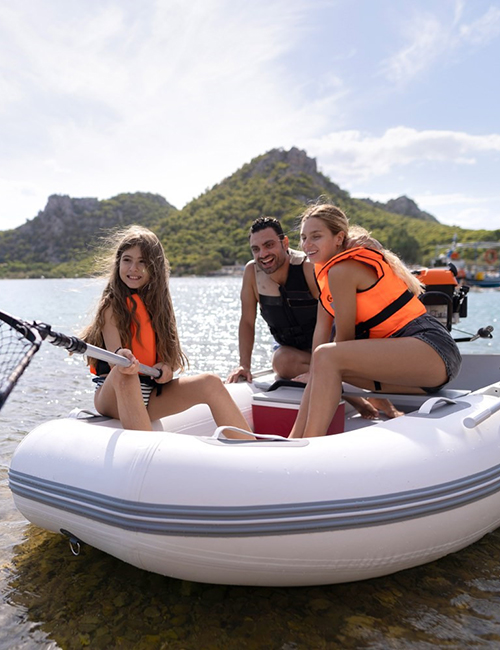
2pcs of aluminum RIB boat designed from Coltonyacht are produced for clients
Introduction :
The production of the 960cm Aluminum RIB boat marks an exciting milestone in the world of recreational boating. This versatile and durable vessel combines the strength of an aluminum hull with the stability and maneuverability of a rigid inflatable boat (RIB). In this article, we will delve into the production process of the 960cm Aluminum RIB, exploring the key steps, materials, and technologies involved. From the initial design phase to the final assembly, we will uncover the intricate details that make this boat a remarkable addition to the watercraft industry.
I. Design and Planning :
The production of the 960cm Aluminum RIB begins with meticulous design and planning. A team of experienced naval architects and engineers collaborate to create a detailed blueprint that encompasses the boat's dimensions, features, and performance capabilities. Factors such as hull shape, deck layout, seating arrangements, and storage compartments are carefully considered to optimize functionality and user experience.
Once the design is finalized, computer-aided design (CAD) software is utilized to create precise three-dimensional models, allowing for virtual simulations and modifications before manufacturing commences. This ensures that the boat meets the desired specifications and performance expectations.
II. Aluminum Hull Construction:
The construction of the aluminum hull is a critical stage in the production of the 960cm Aluminum RIB. Aluminum is chosen for its durability, lightweight properties, and resistance to corrosion in marine environments. The following steps outline the process of creating the sturdy and reliable aluminum hull:
Material Selection: High-grade marine aluminum alloys, such as 5083 or 5052, are selected for their exceptional strength, weldability, and corrosion resistance. Sheets of aluminum are chosen based on the desired thickness and quality.
Cutting and Shaping: The selected aluminum sheets are cut into the required shapes and sizes using precision cutting tools such as waterjets or plasma cutters. Computerized numerical control (CNC) machines ensure accuracy and consistency in the shaping process.
Welding and Joining: The individual pieces of the aluminum hull are then welded together using specialized techniques such as TIG (Tungsten Inert Gas) welding. Skilled welders meticulously join the components to create a robust and watertight structure.
Reinforcements and Bracing: Additional reinforcements such as stringers and bulkheads are integrated into the hull to enhance strength and structural integrity. These components provide rigidity to the hull and distribute stress evenly during operation.
III. Rigid Inflatable Tube Integration :
The next crucial step in the production of the 960cm Aluminum RIB is the integration of the rigid inflatable tubes. These tubes, typically made of Hypalon or PVC fabric, provide added buoyancy, stability, and shock absorption. The following steps outline the process:
Tube Cutting and Shaping: The Hypalon fabric is cut into precise shapes that correspond to the design of the boat's inflated tubes. The fabric is then thermo-welded using heat and pressure to form airtight seams.
Tube Attachment: The inflated tubes are then attached to the hull using a combination of adhesives and mechanical fasteners. This process ensures a secure and watertight connection between the tubes and the hull.
Pressure Testing: Once the tubes are attached, the boat undergoes a comprehensive pressure testing procedure to ensure the integrity and airtightness of the inflatable tubes. This step guarantees that the boat can maintain proper buoyancy and stability even during demanding conditions.
IV. Finishing and Quality Control :
The final stages of production involve finishing touches and rigorous quality control measures to ensure the boat meets the highest standards of performance and safety. These steps typically include:
Surface Treatment: The aluminum hull undergoes surface treatments such as sandblasting, priming, and painting to enhance corrosion resistance and aesthetics. High-quality marine-grade paint is applied to protect the aluminum hull from saltwater and UV exposure.
Installation of Components: Various components such as fittings, navigation equipment, seating, storage compartments, and electrical systems are installed according to the boat's design specifications. This includes the installation of engine mounts and the integration of steering systems.
Quality Control: Before the final assembly, each boat undergoes a rigorous quality control process. This involves thorough inspections, leak testing, electrical checks, and overall functionality assessments to ensure that every aspect of the boat meets the established standards.
Conclusion:
The production of the 960cm Aluminum RIB boat exemplifies the dedication to craftsmanship, innovation, and quality in the marine industry. From the design and planning phase to the integration of the aluminum hull and rigid inflatable tubes, every step in the production process is meticulously executed to deliver a versatile, durable, and high-performing boat. With its robust construction, stability, and maneuverability, the 960cm Aluminum RIB boat is a testament to the seamless integration of aluminum hulls and rigid inflatable technology. Whether used for recreational purposes or professional applications, this boat offers an unparalleled experience on the water.